POWDER COATING
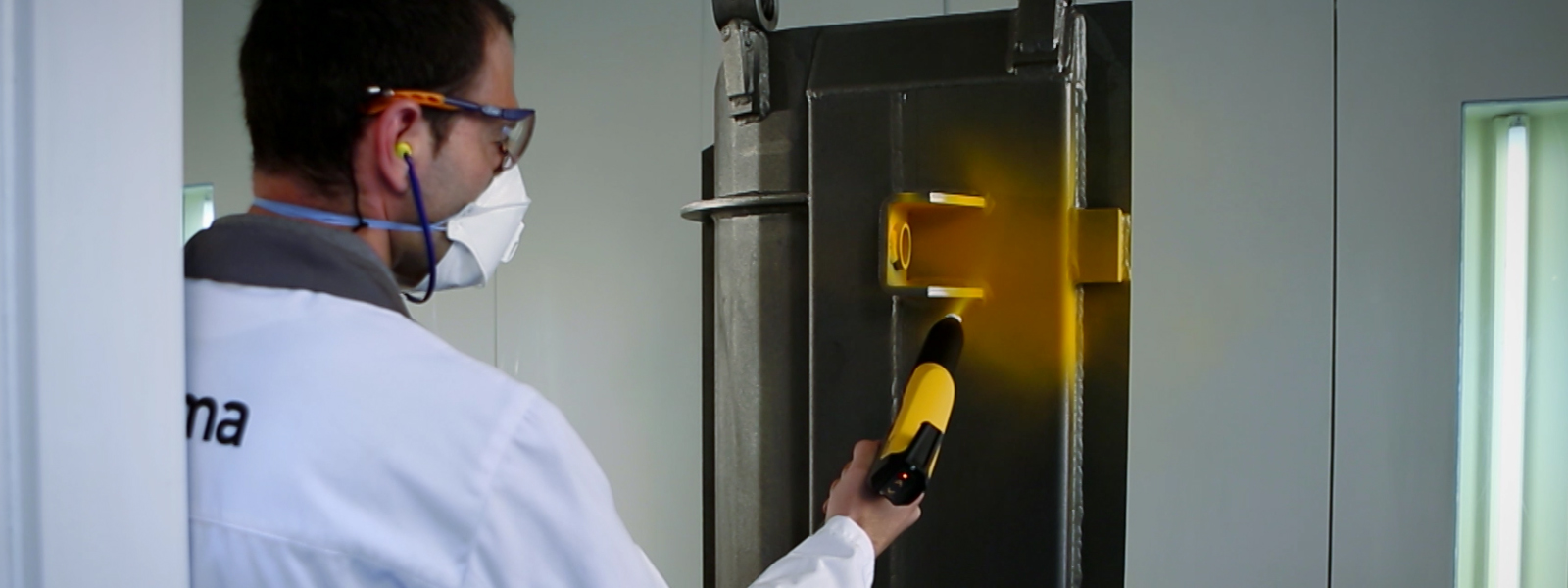
STATE-OF-THE-ART FINISHES
PROFESSIONAL SURFACE COATING
Some surfaces have to look good, some have to be particularly resilient, while others have to meet very specific requirements, or simply be durable. At BRUDER-KELLER, your products will receive the necessary treatment from our proprietary surface treatment equipment. Aesthetics and protection against corrosion go hand in hand at our company. Cooling units that we have manufactured and coated are extremely resilient! Today, the truck may have to cope with the aggressive sea air of Brittany during fish-loading. Tomorrow it will be exposed to the extreme heat and harsh UV light of Spain. Twelve hours later, it will be travelling across the Alps in wind and hail on its way to northern Europe. There is always a danger of stone chipping and it is important to ensure that salty slush cannot damage the surface of our products. Over hundreds of thousands of kilometers, our metal components must cope with all kinds of extreme weather conditions. This is why metal parts produced by us have to prove themselves in a salt spray test lasting 1000 hours. This is only possible when the surface treatment is perfect. Prior to powder coating we can also debur and refine the surface of your products (blasting with sand, corundum and glass beads). After sand blasting has removed rust, scale and other detrimental materials, it can be used to roughen the surfaces and improve the adherence of the subsequent powder coating. Thanks to the use of high-quality surface technologies and optimally trained employees, we can provide a wide range of coating for the surfaces of your sheet metal components and assemblies. Close cooperation with highly effective and efficient partners nearby means we can also provide you with zinc plating, anodizing, galvanizing, bronzing, chromating, pickling and passivation services. ACC (Autophoretic Coating Chemicals), ADP (Anodic Dip Painting) and CDP (Cathodic Dip Painting) are also available. As a sustainable enterprise, we no longer use traditional paints for our coating, as the solvents they release are harmful to the environment. Powder coating, on the other hand, is completely harmless. This is one reason why BRUDER-KELLER decided early on to commit itself to powder coating. Furthermore, powder coating is available in all standard and special colors and in all designs. The range of colors on offer stretches from the German RAL shades of color through the Swedish NCS (Natural Color System) shades to the U.S. PMS (Pantone Matching System) colors. You can also choose from a smooth to a structured surface, and between glossy, satin and matte levels of gloss. On average, the quantity of powder applied will result in a coating thickness of 60 to 120µ. We also provide screen-printing services ourselves. Whether it be single-colored symbols or multicolored lettering and logos, we guarantee that the print and lettering will be perfect. Our experts will ensure that the quality and appearance are top-notch. Authorized external experts regularly check the applied coating’s resistance to corrosion. Unavoidable fluctuations in important process parameters are supervised by means of prescribed and ongoing production controls. Metal test sheets are coated and independent testing institutes examine the protection they provide against corrosion. The success of a powder coating is only guaranteed when surfaces are perfectly clean. At BRUDER-KELLER, we always keep an eye on quality and price. This includes the right choice of chemical cleaning agents, as well as process and plant technology. Our conveyor belt washing system (made only of stainless steel) involves 9 different washing stages including degreasing, three-phase cascade rinsing, spraying with completely demineralized water, iron phosphating, chrome passivation, and a final rinse with clean water (conductivity of not more than 20 microSiemens). Our washing system allows us to deal with components of up to 2,100 mm (length) x 1,700 mm (height) x 800 mm (width) and a maximum weight of 250 kg. Jets and ideal parameters (temperature of the baths varies between 40 and 60° C, automatic dispensing systems for the employed chemicals) mean your components receive ideal preparatory treatment ahead of the subsequent powder coating. Over a total cleaning distance of 41.1 meters, we will “spoil” your components, and with a conveyor speed of 2 meters/minute, the whole process lasts no more than around 20 minutes. For the sake of the environment, our plant operates with zero emissions and without wastewater. It is fed with valuable energized Grander water in order to save on chemicals, energy (propane gas) and maintenance. Furthermore, we only utilize the best available clean-tech innovations, such as reverse osmosis to ensure the conductivity of the baths remains well below recognized limits, and a closed wastewater treatment system that uses steam generators to feed back condensed H₂O into the cleaning cycle. Moreover, we do not use the highly poisonous hexavalent chromium (Cr6+). We prefer to employ lead-free powders. In this way, we satisfy EU guidelines restricting the use of hazardous substances. Our materials comply with RoHS (Restriction of Hazardous Substances) regulations. We also fully comply with the REACH regulation (Registration, Evaluation, Authorization and Restriction of CHemicals), by only using approved chemicals (and only in very small quantities) in our production cycle, and precisely registering and analyzing them.
GEMA Video
Take a “virtual” look at the GEMA powder coating plant that we use. Our Technical Manager will be happy to answer any questions you have about our powder coating plant.