News
BRUDER-KELLER BEGINS PRODUCTION OF STEAM DRYERS
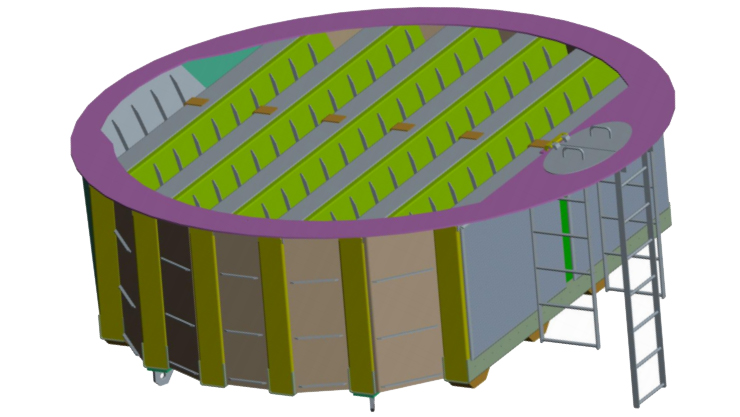
August 2018. BRUDER-KELLER has begun production of 12 steam dryers for large-scale power plants at the company's main facility in Sarre-Union. The units, which will be assembled from 1,795 components, are to be manufactured in a 1000 square-meter production hall that has been specifically expanded for the purpose. As BRUDER-KELLER's General Manager Raymond Keller said at the start of production, the 12 enormous dryers are testimony to what a company can accomplish when a highly motivated workforce takes decisive action using state-of-the-art technology. "BRUDER-KELLER is proof of the international competitiveness of medium-sized companies in the European metal processing industry." The steam dryers under construction in Sarre-Union are intended for use in power plants in France, where they will protect turbines from premature wear and costly damage. Following the ceremonial positioning of the first steel plate, the assembly of the steam dryers will progress step-by-step until they reach their final size of around ø 4.750 m x 2.160 m in height with a dimensional accuracy of +/- 5 mm. Two overhead cranes with a lifting capacity of 25 tonnes will be used in the production process, and the final weight of the each unit will be around 17 tonnes. The start of production was preceded by a planning phase lasting several months. During this period, three-dimensional simulations of the production processes were prepared and controlled using C.A.D.A.M. and the company's own production software. The function and stability of each individual component of the dryer could thus be tested virtually and optimized. Following the start of production, this ingenious digital technology continues to ensure smooth running processes and material flows. "In this way, we can be sure that every component arrives at the right time, and that the production process is seamless and cost efficient," Raymond Keller added.
BRUDER-KELLER Production about to begin for major order
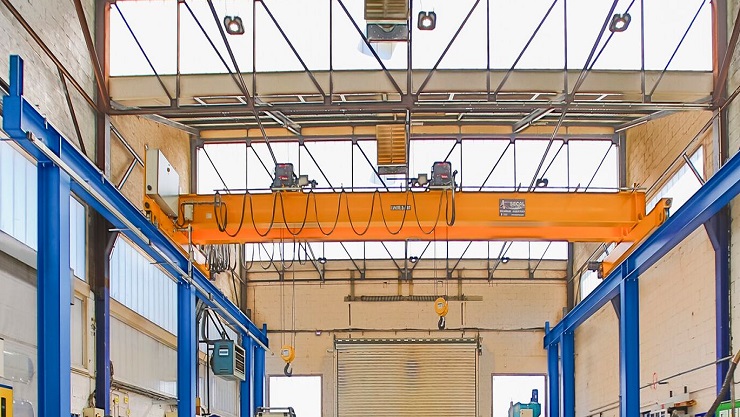
June 2018: Preparations for the production of large nuclear components in the Alsatian town of Sarre-Union have largely been completed. Raymond Keller, Managing Director of the metal processing company BRUDER-KELLER, reports that all the technical specifications are now ready, and the customer has approved the prepared technical drawings, parts lists, manufacturing processes, control and inspection plans. Following the delivery of raw materials, the production of the stainless steel moisture separator is expected to begin early September. The production halls in Sarre-Union had to be converted and technically refitted for the production of such large components (photo).
BRUDER-KELLER to become Smart Factory!
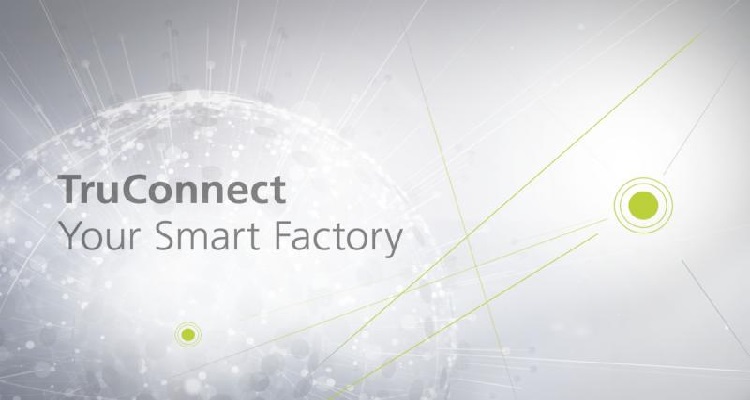
BRUDER-KELLER is to enter the era of Industry 4.0 with TruConnect. After carefully examining all production processes, we have decided to become a Smart Factory in cooperation with the leading German manufacturer of machine tool automation systems. At BRUDER-KELLER in the Alsatian town of Sarre-Union, networked production will begin step-by-step using TruConnect intelligent control systems produced by the Swabian mechanical engineering company Trumpf. On completion, the entire production process will become more transparent, flexible and economical. From autumn 2018, our customers will benefit from Industry 4.0 solutions. In real-time, they will be able to view the processing status of their orders from the moment the order is placed to final delivery, while continuing to profit from high quality and transparent pricing. As a result of the conversion to a Smart factory in Sarre-Union, only a relatively old TRUMPF 5000 will be sacrificed, to be replaced by a more current and higher performing model that is fluent in the language of the future: TruConnect. Be well networked for the future with BRUDER-KELLER!
BRUDER-KELLER TRUCONNECT AND INDUSTRIE 4.0
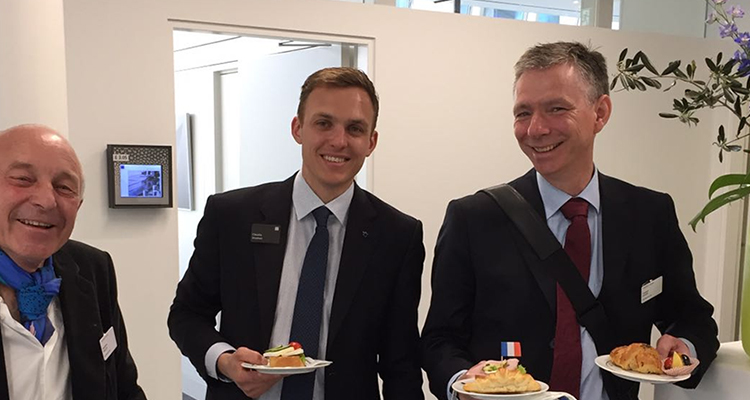
In April, BRUDER-KELLER visited the INTECH 2018 trade show organized by Trumpf under the motto "Industry 4.0" and learned about innovative developments at Trumpf, as well as advances in connected manufacturing. The annual visit to the INTECH in-house trade fair staged by the German machine tool manufacturer Trumpf is a pleasure rather than an obligation for BRUDER-KELLER's management team. Since 1994, we have been making good use of TRUMPF laser technology in Sarre-Union. The then revolutionary TRUMATIC L 3030 was just the beginning, soon to be followed by the TRUMATIC 600, the first TruMatic 7000 in August 2009, and several others since. The laser really is the most flexible tool in existence. Welding, cutting, drilling, milling, bending, curing, fracturing, marking or generation – all these applications are carried out by lasers without the need to produce or modify either molds or tools. Good machines are essential if a company is to be successful. However, as others have good machines too, it is the ability to use them innovatively and economically that makes the difference. As the Managing Director of BRUDER-KELLER it is very important to me that our highly qualified employees work with machines that reflect their abilities and meet their growing needs, if possible tomorrow as well. As a supplier to many different branches of commerce, we are aware of the intensity of the competition faced by our customers. Products are becoming more complex and customized, often at the same time as batch sizes become more variable and smaller. To relieve these pressures on our customers, we are doing our homework and producing efficiency gains that they can benefit from – Key word Industry 4.0. At INTECH in Ditzingen, Trumpf clearly demonstrated what the in-house solution TruConnect and Industry 4.0 will look like in practice. At the entrance, every visitor to the trade fair was able to configure a small sheet metal shell on a Tablet-PC and provide it with a personal inscription. All in all, that made several thousand individual pieces, corresponding to the number of visitors to the fair. While at the fair, every visitor received information on the production status and delivery date of his shell via smartphone-app or mail. Almost effortlessly, it was possible to demonstrate on a small scale what Industry 4.0 means for the customer. And the in-house opportunities are even more impressive: the production manager of a fully-networked manufacturing process can access real-time information on the productivity of his machines on a tablet, while the machine operator controls them remotely using a mobile control app, and the intralogistics manager rebooks stock in the warehouse, while on the move. Furthermore, the maintenance technician can find out the condition of all the lasers in the network at one glance, identify savings potential and optimize the availability and productivity of laser systems. TruConnect isn't the only network solution on the market, but it's certainly a convincing one for metal processing companies. I, for one, can't wait to see future developments from Ditzingen and am already looking forward to INTECH 2019!
BRUDER-KELLER wins major contract for Sarre-Union production site
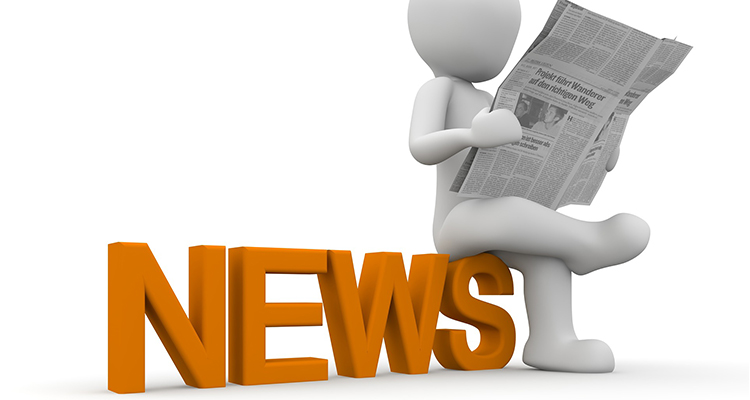
BRUDER-KELLER is going to manufacture 12 enormous water separators over the coming two years and has guaranteed they will be delivered just-in-time. The major power plant contract, which was signed at the end of July 2017, is going to result in a number of changes. "The dimensions and scale of the stainless steel water separators are so large that we are first going to increase the size of the doors to the production halls and install a 25 tonne overhead travelling crane," Managing Director Raymond Keller explained to employees at the Sarre-Union production site. Furthermore, one of the production halls will be completely re-equipped for the special order. "In winning the contract, our investments in highly trained and motivated employees, along with state-of-the-art equipment, have once again paid off," Raymond Keller said.