MACHINERY POOL
Trumpf TRUMATIC 7000 (CNC PUNCHING AND LASERING)
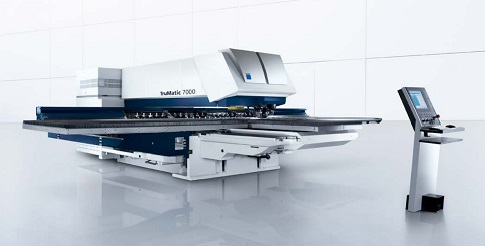
Bruder-Keller is convinced of the benefits of lasering. Early on, we invested in this technology and immediately selected full-option packages and the greatest possible power! With 4000 Watts of laser power and a complete range of accessories, our punch-laser machines for combined processing are capable of meeting every challenge. Whether your products are made of sheet steel, galvanized sheet metal, non-ferrous metals, stainless steel, aluminum, magnesium or other alloys, and whether you need metal sheets that are only 0.5 mm thick, or metal plates with a thickness of 20 mm, our metal processing capabilities know no technical or regional limitations. When it comes to thin sheets, we operate at the highest speeds, while maintaining cutting edges that are burr- and oxide-free. With short setting-up times and no tooling, we provide precise lasering of the finest work-piece contours, even faster punching of diverse hole patterns, and short production times. These clear advantages are economical and of great benefit to our customers. Our investments are always investments in the future of our business partners.
“A high-end combination machine that meets the most stringent demands for part quality, productivity and flexibility.” - Trumpf
Find out more about CNC lasers
- High-speed operation with formats of up to 1,500 x 3,000 mm and plate thicknesses up to 8 mm
- Scratch-free punching and laser processing
- Unique forming capabilities
- Fast-action parts chute for unloading parts
- Efficient and powerful automation
TRUMPF TRUMATIC 5000R (CNC PUNCHING AND NIBBLING)
The first machines came from Switzerland (RASKIN) and the U.S. (STRIPPIT). Then it was Italy’s turn with the stunning SALVAGNINI S4. But with the transition to lean production, we brought in Trumpf machines (TRUMPF 600 L and 5000). The decision in favor of the mechanical engineering company based in southern Germany has proved to be groundbreaking. Bruder-Keller is now using the fifth generation of CNC machines. In the same way our customers place high demands on Bruder-Keller, we place high demands on our machinery pool. As the establishment of the Smart Factory and Industry 4.0 gathers pace, simple programming, flexible handling, high-level automation and complete connectivity are becoming increasingly important.
Find out more about CNC punching and nibbling
- TRUMALIFT SHEETMASTER 1605 for automatic sheet loading, and unloading of completed components
- TRUMASORT RB4 for sorting small work-pieces
- TRUMAGRIP for automatically removing leftover skeletons and strips
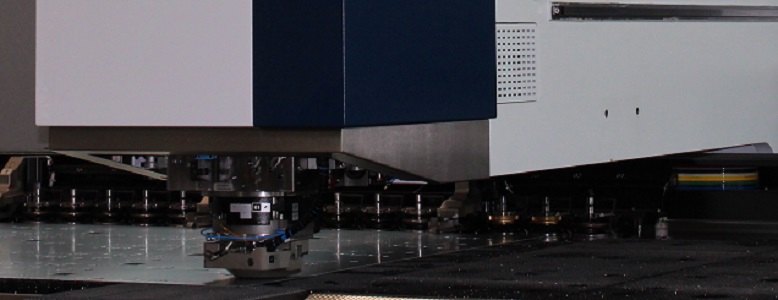
POWDER COATING PLANT
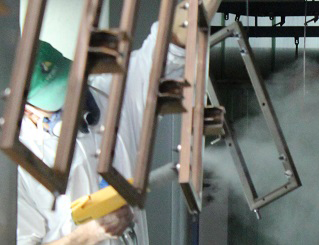
After manufacturing the components that will make up your products, there are several different ways of treating the surfaces. Some surfaces have to look good, some have to be particularly resilient, while others have to meet very specific requirements, or simply be durable. At BRUDER-KELLER, your products will receive the necessary treatment from our proprietary surface treatment equipment. Aesthetics and protection against corrosion go hand in hand at our company. Cooling units that we have manufactured and coated are extremely resilient! Today, the truck may have to cope with the aggressive sea air of Brittany during fish-loading. Tomorrow it will be exposed to the extreme heat and harsh UV light of Spain. Twelve hours later, it will be travelling across the Alps in wind and hail on its way to northern Europe. There is always a danger of stone chipping and it is important to ensure that salty slush cannot damage the surface of our products. Over hundreds of thousands of kilometers, our metal components must cope with all kinds of extreme weather conditions. This is why metal parts produced by us have to prove themselves in a salt spray test lasting 1,F000 hours. This is only possible when the surface treatment is perfect.
Read more about our powder coating plant
- PRE-TREATMENT PLANT (TUNNEL) OTTO MULLER (OMT) Approved dimensions
Length 2,100 x Height 1,700 x Width 800 mm - OTTO MULLER DRYING OVEN (OMT)
Length: 20.82m Throughput time: 10’25’’ Transport speed: 2 m/min - AUTOMATIC EISENMANN POWDER COATING BOOTH with two robots (four guns)
- Automatic GEMA COATING BOOTH with powder recovery system employing cyclones and Absolute filters
- CURING OVEN, heated using propane gas – upstream 112 KW infrared heaters achieve a maximum temperature of 250°C
- POWER + FREE CONVEYOR, programmable with automatic lubrication system, maximum load 250 kg/m
CNC FOAM GASKETING
CNC FOAM GASKETING: Two-component polyurethane systems are used for the manufacture of foam gaskets which are tack-free within a very short time. Seals manufactured in this way are used for soundproofing and to keep out air, dust and humidity.
Gasket dimensions: min. width 5 mm x height 2.5 mm, max. width 20 mm x height 10 mm.
Max. processing dimensions of the system: 1,000 x 2,040 mm
Read more about our CNC foam gasketing system
Further advantages of foam gaskets:- Liquid application prevents shocks
- Good long-term adhesive properties
- Precise placement of gaskets
- High cut resistance
- Protects against many environmental influences
- Compensates large part tolerances
- High resetting ability over long periods
- Suitable for small batches
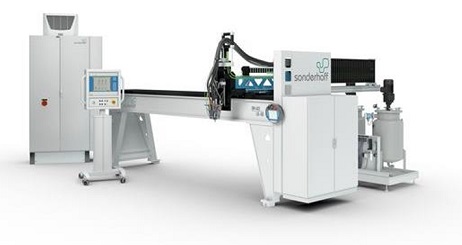
WELDING-SPOT WELDING EQUIPMENT
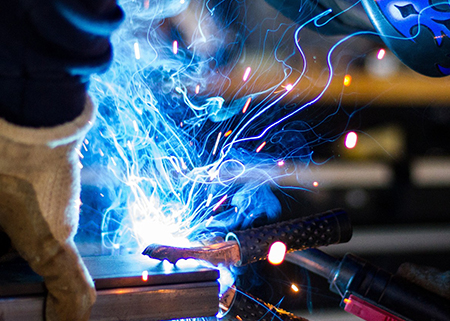
Tried, tested and extremely reliable! At BRUDER-KELLER, the fourth generation of welding robots are already moving in. Since the company was set up in 1966, welding has been one of BRUDER-KELLER’s core competencies. Our numerous welding sources are permanently in use: 22 MIG/MAG welding units, 8 TIG units, 11 spot welding machines and welding guns with a performance rating of 25 to 335 kVa (also usable for aluminum). All our equipment comes from leading manufacturers (ARO, SCIAKY, EWM, FRONIUS). Two 8 axis MOTOMAN WELDING ROBOTS connected to a rotary tilting table are also in use three shifts a day. Furthermore, they can quickly be reset from MAG to MIG or WIG as necessary. Bruder-Keller aims to be one of the industry’s technological pioneers, as it was when it purchased its first robot system from MESSER-GRIESHEIM in 1981.
Find out more about our welding work
- MAG WELDING (Metal Active Gas welding)
- MIG WELDING (Metal Inert Gas welding)
- WIG WELDING (Wolfram Inert Gas welding), including TIG WELDING (Tungsten Inert Gas welding)
- COLD ARC WELDING
- ROBOT WELDING (MAG, MIG and WIG)
- SPOT WELDING